Safe, reliable and competitive gas supply solutions
Solutions for the metal industry
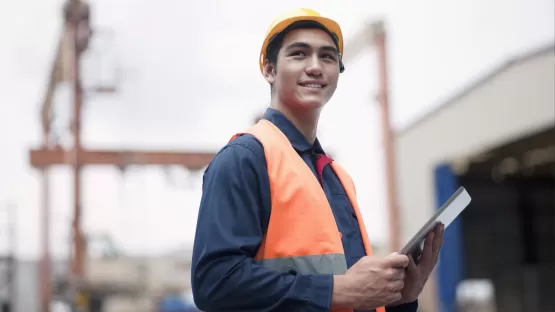
Global network
Air Liquide is a leader in the production and supply of high-performance industrial gases for the metal industry, such as oxygen, nitrogen and argon.
An international network of Air Liquide experts, specialized in the metal industry, is ready to support you.
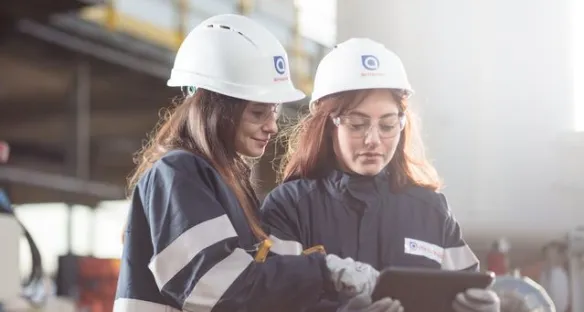
Tailor-made solutions
Our teams will work with you to find the most suitable and most cost-effective solution for your gases, depending on the desired purity and volume of consumption.
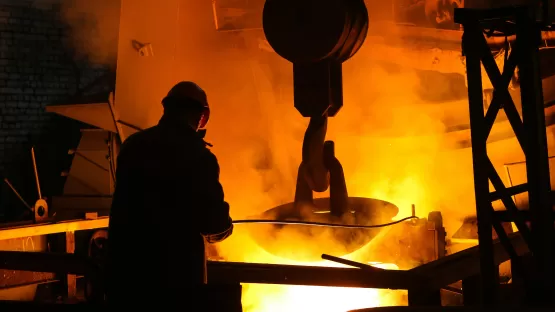
Steel fabrication
The production process of steel requires large quantities of industrial gases, which Air Liquide supplies via pipelines or by truck. If necessary, Air Liquide also provides the necessary equipment to be able to make gases on site.
In addition, Air Liquide offers a wide range of technical solutions for blast furnaces, converters, ladles and reheating furnaces.
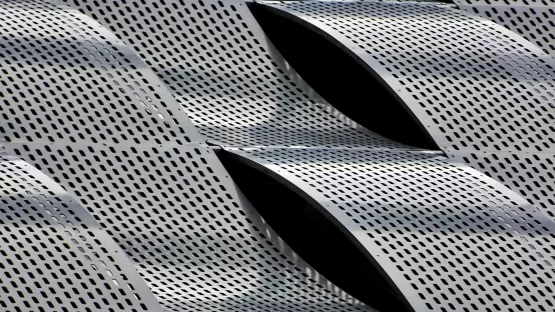
Non-ferrous metal processing
Many production processes of non-ferrous metals (aluminium, lead, copper, zinc, nickel, cobalt, gold, etc.) make extensive use of industrial gases: ore concentration, in-situ leaching, concentrate treatment and primary metal refining.
Industrial gases are also suitable for purifying waste water, so that the consequences for the environment are limited as much as possible.
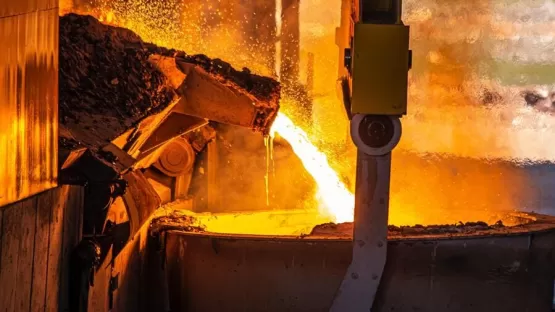
Fonderies (ferrous and non-ferrous metals)
Our solutions address all stages of casting production, from metal melting to work piece finishing and mold maintenance.
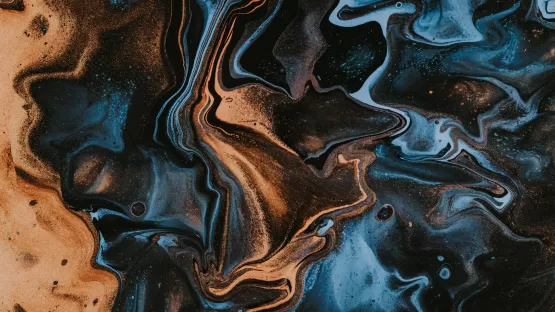
Primary metal processing
Primary metal processing operations aim to provide products in forms suitable for the production stages of the final parts while of course preserving the initial qualities of the metal.
Industrial gases will thus contribute to preserving the intrinsic qualities of metallurgical products through metal shaping operations: rolling, wire drawing, drawing, hot forming. The solutions offered cover all ranges of annealing and tempering of steels and non-ferrous metals and guarantee decarburisation against oxidation.
The proposed solutions also contribute to compliance with the target temperature profiles, in the temperature rise steps and the cooling steps.
The use of high pressure nitrogen or argon is necessary to obtain quality metal powders by pressurised atomisation of liquid metal.
Stainless steel production
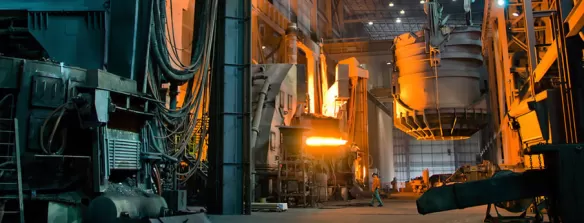
The AOD process is the most used in the world for the production of stainless steels.
This method required the implementation of gas injection sequences (Argon, Oxygen, Nitrogen) with high pressures and high peak flow rates.
Air Liquide offers steelmakers the supply of gases and associated facilities corresponding to their specific needs.
Liquid metal refining
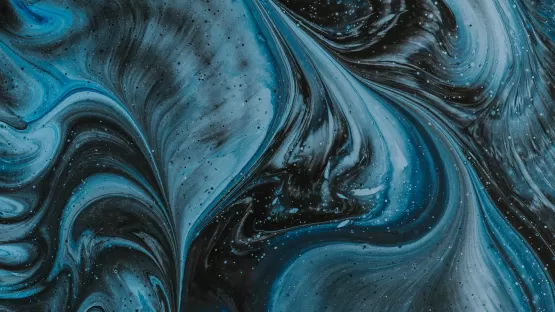
Gases (nitrogen, argon) play an essential role in the refining operations of steel, cast iron, light alloys and in obtaining a liquid metal that meets the required specifications: composition, homogenity, inclusion and cleanliness.
Business specialists provide you with advice for the implementation in complete safety: injection system, control and regulation of gas flows.
Inerting of liquid metal
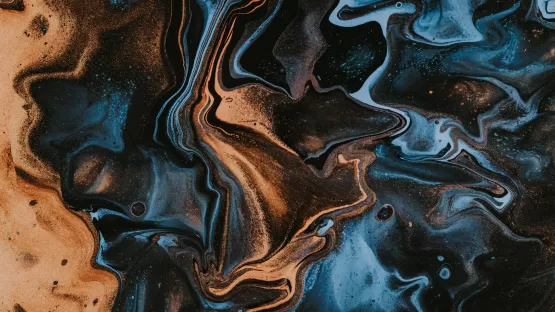
Air Liquide specialists metallurgical customers in adapting and implementing the technologies developed by Air Liquide in their specific industrial context.
To protect the liquid metal from oxygen absorption and the formation of oxides, inerting solutions using nitrogen or argon must be deployed in specific technical environments: high temperature, reduced accessibility operations and continuous industries.
Heating and maintaining temperature
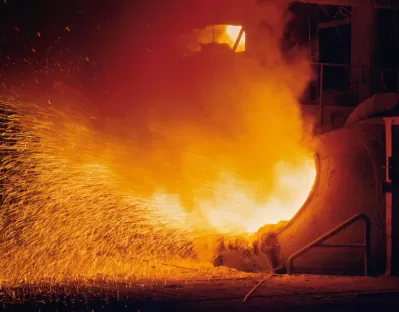
The oxycombustion technologies developed by Air Liquide for the reheating operations of slabs, sheets and in general, primary processing metallurgical products contribute to increasing the productivity of furnaces, improving energy efficiency, reducing emissions of Co2 and drastically reduce nitrogen oxide (N2O) emissions.
The preheating of transfer ladles with oxy-fuel furners brings great flexibility to industrial liquid metal transfer operations on a daily basis.
The safety of facilities is a top priority.
Primary elaboration of non-ferrous metals
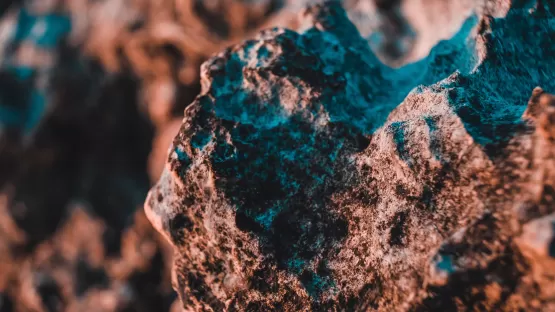
Industrial gases, first and foremost oxygen, but also argon, nitrogen and sometimes carbon dioxide, hydrogen and air are used in the primary production processed for metals from metal ore concentrates.
The implementation solutions are very diverse and concern the pyrometallurgical and hydrometallurgical sectors. Air Liquide has expertise in the impact of gas (Nitrogen, Oxygen, Air) used in the ore concentration process by flotation.
If the concentrate processing sector is of the pyrometallurgical type, Air Liquide offers you its solutions with oxygen and/or nitrogen for the melting, conversion and refining phases. If the chosen process is the hydrometallurgical type, Air Liquide offers you its solutions with oxygen, air and/or carbon dioxide for your leaching, residue treatment and pH control phases.
Air Liquide's business experts support customers from the upstream phases - feasibility studies, tests, demonstrators -, in the detailed study phases and implementation of new facilities as well as during the operating phase to meet the performance, energy efficiency, environmental impact reduction and productivity objectives.
Finally, oxygen-assisted in-situ ore leaching solutions are implemented in cases of low-grade deposits such as uranium deposits.
Smelting and recycling of non-ferrous metals
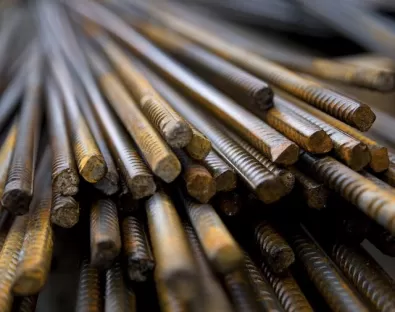
Solutions adapted to non-ferrous metal recycling channels contribute to achieving the objectives or selective recyclability, productivity, energy efficiency and reduction of environmental impact.
Controlled oxy-combustion solutions meet the needs of recycling channels in generalised remelting furnaces for the recycling of aluminium, lead and copper.
Hydrometallurgy solutions meet the more specific needs of selective extraction of many non-ferrous metals such as copper, tin & nickel.
Molding & finishing
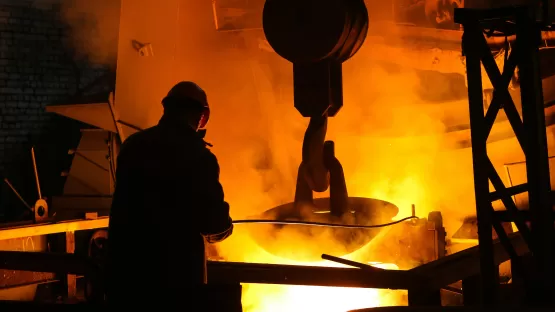
We ensure the supply of industrial gases and implementation solutions for ferrous and non-ferrous metal casting technologies (casting machines, chill casting, investment casting and sand casting, etc).
More specific solutions also use industrial gases:
- Deburring of parts
- Cleaning of molds wit projection of solid carbon dioxide
- Lubrication of molds by carbon deposit produced from acetylene