Guarantee of the quality of your powders
The gaseous atomisation stage of metal powders requires controlling the purity of the gas used to limit oxidation, in particular of the most sensitive metals such as titanium. Similarly, an inert atmosphere protects the powders from moisture and oxidation during storage or recycling.
Gas atomisation: A demanding process
The gas is at the heart of the atomisation process with pressures that can reach several tens of bars, a temperature of several ºC.
Security
Depending on the heat treatments, the atmospheres considered may contain, for example, hydrogen, hydrocarbons or use methanol for cementation. Strict compliance with the safety rules in force is essential.
Use of metallic powder
Powder is the ally of many additive manufacturing processes. Air Liquide gives you the technical specifications of powders for industrial use.
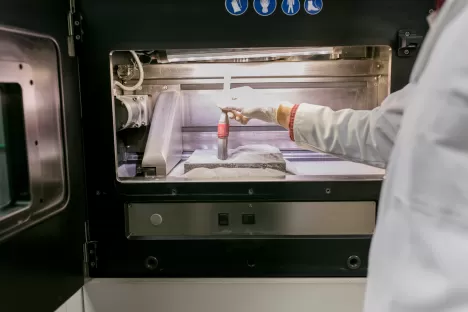
Technical specifications of metal powders
Many industrial additive manufacturing processes use powder: Of course, powder bed fusion (Powder Bed Fusion) whether by selective laser sintering (Selective Laser Sintering or Selective Laser Melting) or by electron beam ( Electron Beam Melting), but also certain material deposition processes under concentrated energy (Directed Energy Deposition).
The technical specifications of metal powders are generally tight and obviously depend on the requirements of end customers. There are several key factors:
- The chemical composition related to metallurgy often has a low level of oxidation: in particular for titanium alloys driven by the demand of the aeronautical or medical industries, or nickel bases.
- A fine particle size distribution (PSD) adapted to the process (usually centered around 40µm for SLM, 80µm for EBM) - and to operating requirements, compromise between productivity and final surface condition improved by more powders thin.
The morphology of the powders: a form factor as close as possible to the sphere, the absence of satellites
Some of its specifications are related to macroscopic tests such as the measurement of density or flow rate, others require microscopic examination.
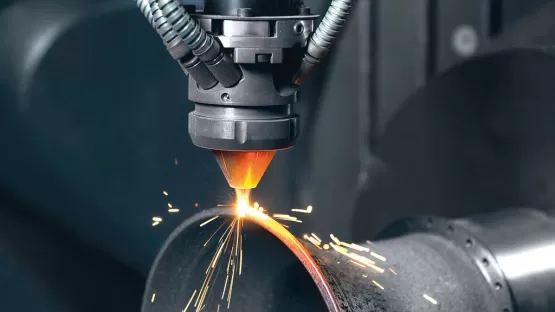
Gas atomisation
Gas atomisation is the most widely used process to manufacture metal powders for additive manufacturing. Several technologies exist (EIGA, VIGA, Plasma) but as its name suggests, they all use gas.
A jet of high pressure gas - argon or nitrogen depending on the material - sprays small droplets of a liquid metal.
Only a suitable implementation of the gas will allow you to reach your production objectives with the required quality. The pressure - several tens of bars -, the purity, the temperature - up to several hundred degrees - are critical, for example to be more specific on small particle sizes.
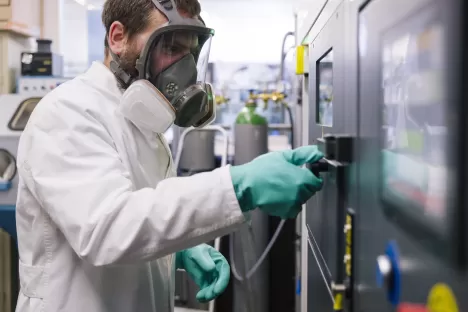
Storage and recycling
In addition, the fine grain size and reactivity of certain materials such as aluminum or titanium can create a risk of explosion requiring flammability prevention measures, which are added to operator protection measures.
Thus, during the handling of the metal powder, from transport to storage, passing through de-powdering or sieving after printing, the powders require a protective inert atmosphere which also protects against untimely oxidation and moisture absorption.
The new ASTM / ISO 52907 standard recommends inerting powders. Argon or Nitrogen can be used depending on the materials.
Through its expertise, Air Liquide will be able to support you and define with you the best installation to meet your needs.
Air Liquide supplies the gases at the purity required for each additive manufacturing application.
Phase | Process | Molecules | Gas intensity | |
---|---|---|---|---|
Metals | Gas atomisation | Production of metal powder | Ar for high intensity alloys such as titanium | Very high |
Additive manufacturing | Selective Laser Melting (SLM) | Ar, N2 | Medium | |
EBM Process | He | Very low | ||
Wire Arc Additive Manufacturing (DED) | Ar and Ar mixtures | High | ||
Laser Metal Deposition (DED) | Ar | From low to high | ||
Binder Jetting (sintering) | Ar-H2, N2 mixtures | Medium | ||
Management of metal powders (logistics, storage, sieving) |
Ar, N2 | Low | ||
Post-treatment | Heat treatment (tempering) | Ar, N2 | Medium | |
Hot Isostatic Pressing | Ar | High | ||
Parts cleaning | Cleaning with dry ice or supercritical CO2 (to be considered) | Low | ||
Other materials (polymers) |
Additive manufacturing | SLM process | N2 (consider generators) | Low |
Wire extrusion | N/A | N/A |
Gases used throughout the additive manufacturing process
The main gas used for the manufacture of metal parts is argon, but depending on the materials and processes, nitrogen or helium can also be used. These gases must, of course, be used under controlled conditions in terms of safety (e.g. risk of anoxia), in a professional setting.
Do you have any questions about powder in additive manufacturing?
Please complete our contact form below and we will get back to you as soon as possible.Production of metal powders by atomisation
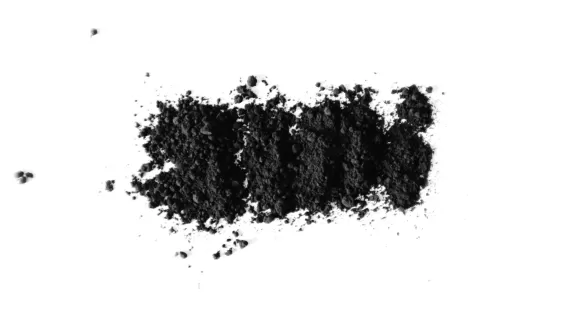
“Direct manufacturing” channels (sintering, MIM, additive manufacturing, etc.) rely on the use of metallic powders with specific characteristics.
The powders are obtained by atomisation under gas (argon, nitrogen, helium) in installations where the gases are injected at high pressure, much higher than conventional distribution pressures.
Air Liquide will then intervene:
- From the pre-project phase to define the general diagram of the installation
- And provide a facility that meets production requirements