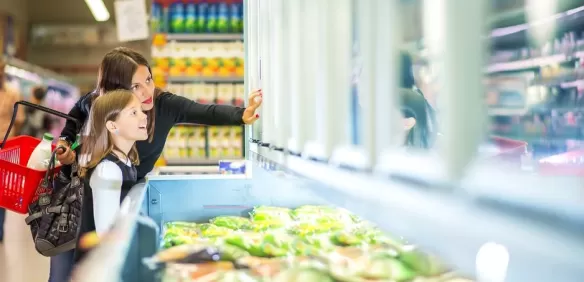
What are the different packaging machines for M.A.P?
Discover the different types of modified atmosphere packaging machines suitable for different types of MAP.
Depending on the characteristics of your food products and the requirements of your market (distribution channel, marketing requirements) different types of packaging are possible: prefabricated bags, thermoformed bags, prefabricated rigid trays or trays, thermoformed rigid trays or trays.
How to choose between a gas sweeping machine and a vacuum-compensated machine?
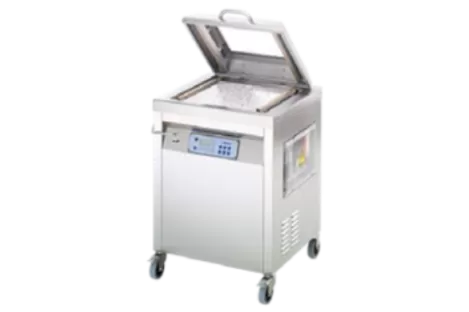
Are you starting out in MAP? Bell machines meet your needs.
- with manual operation,
- a production capacity of 2 to 3 cycles/min,
- residual oxygen level < 1% (depending on vacuum pump power and vacuum time).
This is the vacuum-reinjection start-up solution (monthly consumption: approximately 50 m3 / month).
To determine your gas requirement, it’s simple: 1 volume of gas for 1 volume of bell. The number of bags or trays per packaging cycle depends on the size of the bag and the cover.
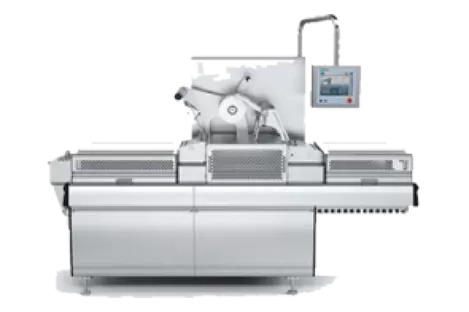
For higher production rates: opt for traysealers or thermoformers
The traysealers
- semi-automatic, they are integrated into the online process,
- speed higher than that of bell machines,
- recommended for rates lower than 2000 trays/day,
- residual oxygen level < 1% oxygen
- gas consumption: between 100 to 500 m3 / month.
- your gas requirement = packaging volume x3.
Do you want to package your products in bags?
Scanning machines, vertical bagging machines (VFFS for vertical Form Fill Seal) or horizontal bagging machines (HFFS) meet your needs! Dedicated to products that cannot withstand vacuum, these machines are capable of creating sachets from a single reel of film. The atmosphere being supplied by gas sweeping, the gas requirement will be greater than on a vacuum reinjection machine.
- automatic operation,
- machines integrated into the process,
- the rates are very high: from 60 to 120 strokes per minute.
This technique does not make it possible to achieve levels of 1% oxygen but rather 3%.
This type of machine is reserved for products supporting these O2 contents. To obtain these contents, on average it is necessary to inject 3 to 8 volumes of gas / total volume of sachet.
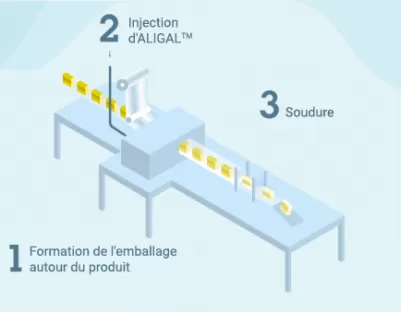
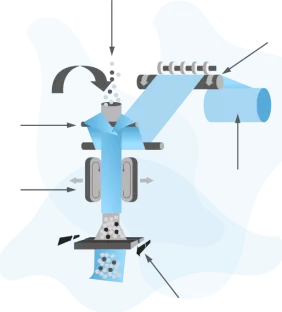
For products sensitive to oxidation, choose compensated vacuum
Depending on the packaging machine technology used to carry out packaging under a protective atmosphere, the residual oxygen level and gas requirements will be different:
- Compensated vacuum or re-injection vacuum (sealer, chamber machine, thermoformer), the residual O2 rate will be < 1% and the gas requirement: 1 gas vol / chamber volume,
- Gas sweeping (horizontal or vertical bagging machine), the residual O2 rate will be < 3% and the gas requirement: 5 gas vol / volume of the bag.
For products that are particularly sensitive to oxygen, it will therefore be preferable to favor machines with compensated vacuum or vacuum reinjection in order to ensure a minimum oxygen content in the packaging at the time of packaging.
In the particular case of “breathable” products such as fruits, vegetables, 4th range products, packaging in a protective atmosphere is carried out with a perforated or micro-perforated upper film. This ensures a balanced atmosphere (EMAP) thanks to gas exchanges between the atmosphere of the packaging and the environment.
The + from Air Liquide experts
So to choose the right packaging machine, you should take into account:
- the nature of the product and the desired appearance of the finished product,
- the expected pace,
- the desired level of automation,
- the nature of the packaging and/or film: barrier properties of the packaging,
- the target residual oxygen level and the desired vacuum level,
- gas consumption (in reinjection or gas sweeping).
Do you have questions about the different packaging machines for M.A.P? Please fill out our contact form.
Our experts will respond to you within 24 hoursFrequently asked questions
How to increase the shelf life of products?
What does “packaged in a protective atmosphere” mean on certain food packaging labels?
What are the different packaging machines for M.A.P?
What installation do I need to use gas?
What modified atmosphere for the conservation of fresh meats?
What modified atmosphere for bakery products?
What modified atmosphere for the conservation of seafood products?
What modified atmosphere for the conservation of cheese and dairy products?
What modified atmosphere for dry products?
What modified atmosphere for the conservation of prepared fruits and vegetables?