Why use oxy-fuel for melting steel, cast iron or non-ferrous metals?
|
Energy savingThe use of pure oxygen instead of air improves combustion efficiency and reduces fuel consumption. By replacing air with oxygen, energy is saved and the volume of flue gases is reduced, since there is no nitrogen to heat. |
|
Improved furnace performance and reduced emissionsOxygen combustion improves the flexibility and stability of furnace operations, and removes nitrogen from your furnace, thus greatly reducing emissions. In fact, the NOx level is more than 10 times lower than with air combustion. |
|
Improved quality of the final productBy improving the flexibility and stability of furnace operations, the quality of what is produced is improved. |
|
Reduction of investment expenses (CAPEX)Equipment for preheating small volumes of combustion oxygen is less expensive than equipment for preheating larger volumes of combustion air. |
|
Productivity increase
|
|
Extension of the useful life of your facilities
|
Our oxyfuel solutions for the metal industry
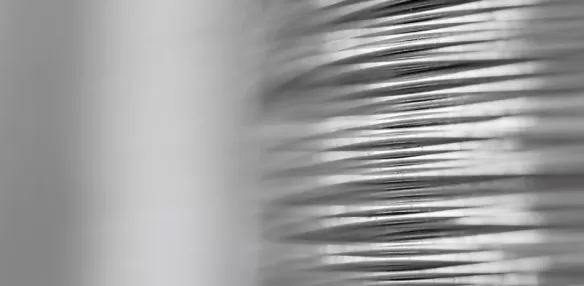
BOOSTAL™ Oxy-fuel for non-ferrous metals
Are you a non-ferrous primary smelter, foundry, secondary smelter and refining professional looking to reduce air emissions, reduce your carbon footprint and/or increase your productivity?
Metals that are sometimes recycled and have varying levels of volatile organic compound (VOC) contamination are often melted in reverberatory furnaces and rotary kilns equipped with regenerative burners to reduce energy consumption by preheating combustion air. The combustion of air generates atmospheric emissions that will not allow the environmental objective of carbon neutrality to be reached in 2050.
We propose an oxy-combustion technology that consists of injecting pure oxygen instead of air into the raw material to be melted . Oxyfuel burners improve heat transfer efficiency, which speeds up melting and increases productivity.
In the absence of nitrogen, the volume of combustion oxygen is less than that of the combustion air. This reduces the amount of energy needed and consequently the NOx and CO2 emissions.
BoostAL™ for non-ferrous metals offers you a suitable and environmentally responsible alternative to regenerative air burners.
Environmental benefits
- Up to 90% reduction in NOx emissions.
- Up to 50% reduction in CO2 emissions
- Up to 50% fuel savings.
Operational benefits
- Up to 50% increase in productivity.
- Reduced capital expenditures for flue gas treatment with a 5-fold reduction in volume to be treated.
- Higher yield of recycled metals.
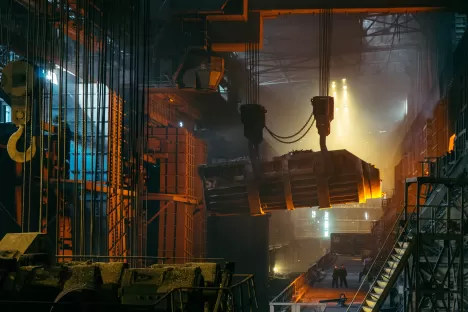
BoostAL™ for Iron casting in rotary furnaces - Foundry and casting industries
Rotary furnaces are used to produce all grades of gray and ductile iron. Historically, oxygen from combustion air was used to melt metal.
However, being a thermal ballast, the nitrogen in the air limits the combustion temperature to 900°C.
When melting in a rotary kiln, all the thermal radiation accumulated in the refractory lining is transmitted to the metallic load with the rotation of the kiln.
The use of pure oxygen increases the temperature of the flame to 1,500 °C, which allows more energy to be transferred to melt the metal.
We offer an oxy-combustion technology that combines oxy-combustion burners and oxygen injection directed to the molten bath in which a solid fuel (anthracite) is added.
BoostAL™ for melting molten iron in rotary kilns reduces atmospheric emissions, greatly speeds up melting time, increases productivity, reduces capital costs (smaller filter unit), and improves metal yield.
Environmental benefits
- Up to -90% NOx emissions
- Up to -60% CO2
- emissions Up to 60% fuel savings
Operational advantages
- Increased productivity
- Reduction of cycle time of up to 30%.
- Reduced capital expenditure
- Volume of flue gas to be filtered divided by 4
- Increased metal yield
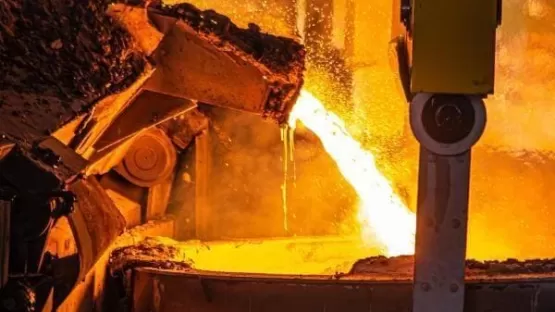
BoostAL™ for melting iron in cupola furnaces - Foundry industry
Cupola furnaces are vertical furnaces designed to produce all grades of gray and ductile iron. Air is injected from below to burn the solid coke, which in turn transfers the heat to the metal charge.
However, being a thermal ballast, the nitrogen in the air limits the combustion temperature to 900°C and the performance of the dome. This limits the productivity rate, the melting temperature and restricts the scrap supply.
To overcome these limitations, the use of pure oxygen increases the temperature of the flame to 1,500 °C, which allows a greater transfer of energy for the fusion of the metal.
We offer a wide range of oxy-fuel technologies for different levels of oxygen enrichment combining lances and dome oxygen injection.
With BoostAL™ to melt iron in cupola furnaces, three ways are possible:
- Oxygen enrichment of the combustion air that modifies the thermal gradient in the combustion zone, increasing the maximum temperature. It is used for the low oxygen enrichment (2%) of the combustion air, in all dome sizes.
- Injection of oxygen through lances in the combustion zone of coke with enrichment indexes higher than 2%; the oxygen is injected directly into the cupola and allows a better penetration of oxygen in the center of the cupola and a better distribution of it.
- Oxygen injection by means of supersonic lances for hot air domes for the penetration of oxygen in the center of the dome thanks to an injection speed twice as high (momentary force of oxygen=230N) than the previous one.
Environmental benefits
- Coke reduction: up to 5-10% kg of coke/tonne of iron
Operational advantages:
- Productivity increase up to 7% at 1% for every % oxygen enrichment
- Casting temperature increase up to 10°C to +15°C per % oxygen enrichment
- Increased operating range up to +30% to +50% of nominal output at 3% oxygen enrichment.
- Increased metal yield
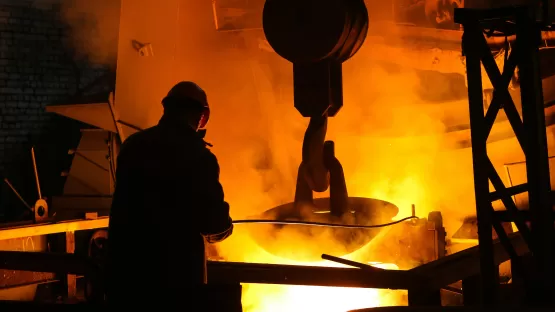
BoostAL™ Oxy-fuel for preheating liquid metal transport ladles
Looking to reduce air emissions, lower your carbon footprint, or increase your productivity?
Liquid metal transfer ladles are preheated to:
- Minimize thermal shock when pouring molten metal;
- Prevent damage to the refractory lining;
- Reduce metal temperature drops in the ladle.
Ladle preheating is generally done using air combustion, while it is limited to a maximum metal temperature of 1000°C and is very fuel intensive.
BoostAL™ Ladle Heating is Air Liquide's complete offering for preheating ladles in steel mills and foundries.
We offer advanced oxy-fuel technology which, thanks to high oxygen/fuel radiative combustion:
We offer advanced oxy-fuel technology which, through strong radiative combustion of oxygen/fuel
- Accelerates the heating of the refractory surface up to 4 times, at a temperature (defined by the customer) that prevents overheating of the metal at the exit of the furnace,
- Simultaneously cleans accumulated oxide pockets on the refractory surface and improves metal quality by eliminating thermal stratification in the pockets,
- Increases the life of the refractory lining,
- Dramatically reduces NOx formation by removing nitrogen,
- Reduces CO 2 emissions up to -60% and fuel consumption up to -40%