Why choose Air Liquide's oxy-fuel offerings for flat glass, technical glass or container glass?
|
Save energyUsing pure oxygen instead of air improves combustion efficiency and reduces fuel consumption, thus saving energy and reducing flue gas volume since there is no nitrogen to heat. |
|
Optimise your processes and reduce polluting emissionsCombustion with oxygen improves the flexibility and stability of the combustion process. In addition, CO 2 emissions are reduced and the presence of nitrogen in your oven is eliminated, thus greatly reducing NOx emissions (level more than 10 times lower than with combustion with air). |
|
Improve the quality of your productsThe stability of the furnace operations ultimately improves the quality of the glass that is produced. |
|
Reduction of investment expenses (CAPEX)Equipment for preheating small volumes of combustion oxygen is less expensive than equipment for preheating larger volumes of combustion air. |
|
Productivity increase
|
|
Extension of shelf life of your facilities
|
Our oxy-fuel solutions for the glass industry
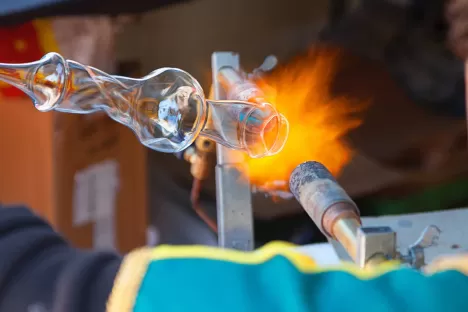
Oxy-fuel for glass melting
Looking to reduce emissions? Do you need to reduce your carbon footprint?
Air is commonly used to provide oxygen in industrial glass melting furnaces. Oxy-fuel technologies offer the potential to reduce air emissions and fuel quantities, maintain production capacity and provide flexibility. These processes are based on the replacement of air by oxygen.
No energy is wasted heating nitrogen in the air, which is useless in the combustion process and generates unwanted NOx . In addition, fewer CO 2 emissions are produced due to lower fuel consumption. Our advanced oxy-fuel combustion (or oxy-fuel combustion ) technologies provide optimal glass melting conditions and improve heat transfer.
Benefits:
- Up to 90% NOx reduction
- Up to 45% CO2 reduction
- Up to 40% fuel savings
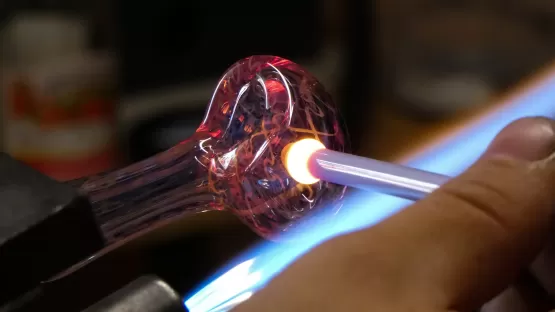
Oxy-Boosting for glass melting
Do you want to increase the productivity of your furnace?
Looking to maintain your production in case your regenerators deteriorate?
A furnace is rebuilt every 8 to 15 years. A few months or 1-2 years early, glassmakers can face plugging of their furnace regenerators, resulting in a significant reduction in productivity. Boosting glass melting with oxygen is the best way to increase or maintain productivity. There are 3 solutions:
- Enrichment of the air with oxygen to continue using the air burners while increasing the oxygen concentration in the combustion air (typically up to 24%)
- Oxy-boosting by injecting pure oxygen through one or more lances inserted in or near the air burners
- The addition of oxy-fuel burners when a glass furnace temporarily or continuously needs increased heat transfer.
Benefits:
- Up to 10% increase in productivity
- Longer oven life
Gas, equipment and services for oxy-combustion and oxy-boosting
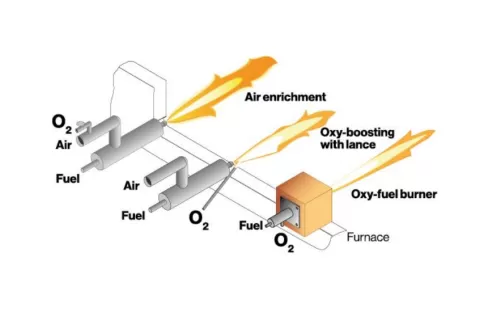
From oxygen supply to process optimization, you'll benefit from the equipment and services associated with our oxyfuel glass melting technologies. They are suitable for all types of glass, including fiberglass, reinforcing fiberglass, lighting glass and other technical glass.
- Liquid oxygen supply or on-site production
- Combustion equipment
FLAMOXAL-B is an automated control system for monitoring oxy-fuel burners and their feed systems.
Patented burners:
- The STANDARD BURNER FOR MELTING is an oxy-combustion burner not cooled by water, specially designed for continuous melting furnaces. It is suitable for most types of glass.
- The FC BURNER FOR MELTING in which fuel and oxygen are mixed outside the burner block. They are then fed into the furnace through injectors that produce an extremely bright flame that is up to three times wider than conventional oxy-fuel burners.
- The VM BURNER FOR MELTING generates a variable amount of energy and is particularly suitable for narrow furnaces.
Experts at your service
Based on your specifications, our experts define the best combustion technology for your furnace. They support you at all stages of your project:
- From auditing your current foundry process to flue gas analysis and thermal and mass balance with our AIRLOG software,
- During preliminary and detailed studies of your new solution and during the installation and commissioning of the equipment.
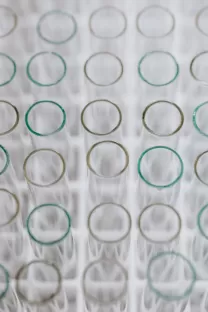
Oxy-formed for glass
Do you want to improve the quality of your glassware? Looking for a safer way to move glassware into the polishing stage? Looking for a more environmentally friendly process
Lubrication of IS machine transfer belts can be achieved by depositing a carbon film from the thermal decomposition of a hydrocarbon. The automated lubrication method provides excellent surface quality to glassware, preserves the quality of the workplace atmosphere, and reduces the risks and time-consuming task of manual grease lubrication.
Air Liquide offers equipment for the supply and decomposition of the hydrocarbon as close as possible to the surface to be lubricated, as well as the hydrocarbons that can generate this carbon deposit.
The ALBLACK solution , designed and adapted to your specific needs and based on our revolutionary technology, uses pure oxygen, acetylene and natural gas . It is an automatic lubrication system. Lubrication is achieved by depositing a thin layer of carbon produced by cracking acetylene in a high-temperature flame from an oxy-fuel burner.
- Quality improvement: The fine carbon layer of 10 to 100 microns, which burns immediately, leaves no residue.
- Safe transfer of glassware to polishing stage: Carbon black coating prevents glassware from falling off as it moves to the finishing stage. This reduces rejection rates by up to 2% to 3%.
- More environmentally friendly process
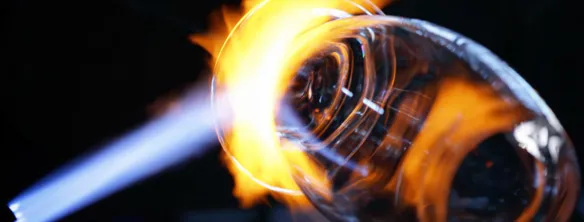
Oxy-finish for glass
Do you want to improve the quality of your glass? Looking to improve your productivity with a greener process?
After forming, the glass can undergo finishing operations such as cutting, edge blending or polishing.
Oxy-combustion is a state-of-the-art technology that replaces the use of abrasive powder or acids for polishing. It is a proven technology that reduces fuel consumption by up to 80%, while requiring less preheating and processing time.
Burners can be installed on your production line if you want to prevent distortion when preheating your item. Air Liquide's polishing technologies remove surface defects and improve production performance.
Environmental benefits
Hazardous liquids are not used and waste is not treated
Operating benefits
- Elimination of defects during molding with the elimination of marks and sharp edges
- Addition of brightness, transparency, luminosity
- No noise
- Higher production rate : fewer defects in your articles
- Flexible solution: adaptable to different shapes and sizes of your articles Packaging transformation ordinary glass into prestige finished products