Are you considering the implementation of a material deposition process under directed energy flow? Are you looking for the best gas to provide protection against oxidation and humidity?
1- Productivity & reproducibility
Thanks to a choice of gases (Argon, nitrogen and helium) of high purity, and to an efficient distribution installation, your processes are optimized (stable and without drifts). You can thus maximize speed and yield, while maintaining a result and a final structure of perfect quality from one layer to another and identical deposit characteristics all along the bead.
2- Flexibility & reliability
Air Liquide adapts the mode of gas supply according to the development of your activity, and implements the means to ensure a continuous and secure supply. In some cases, Air Liquide can offer to equip your facilities with sensors and analysers to monitor your production.
3- Gas safety
Air Liquide guides you to ensure the safety of installations, and advises you on the implementation of anoxia detection equipment, installation maintenance services, not to mention training on the use of gases.
4 - Expertise
Drawing on its experience, Air Liquide supports you at every stage of your project: from the definition of your specifications and the design of network and security installations, to assistance with the start-up of your manufacturing processes. Our extensive offer allows you to benefit from innovative solutions across the entire metal additive manufacturing value chain.
Our gas solutions to optimise the performance of your Laser Metal Deposition (LMD) and Direct Metal Deposition (DMD) deposition processes
With Air Liquide, benefit from supply solutions adapted to your manufacturing process, combining gas, distribution installation and technical expertise.
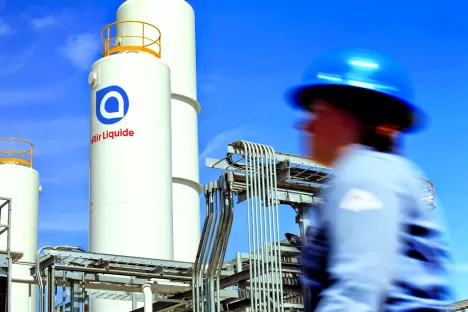
Your gas supply for direct laser processes (LDM or DMD)
The most used gases are Argon (Ar), Nitrogen (N2) and Helium (He).
The high purity of these gases is often required due to the requirement of laser metal processes.
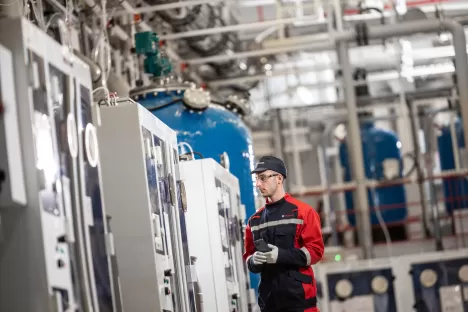
Your gas distribution installations
On the strength of its experience, our engineering offers you to design and build your installations in compliance with safety rules, to ensure perfect reliability, maintainability, and the continuity of supply required by laser metal deposition technologies.
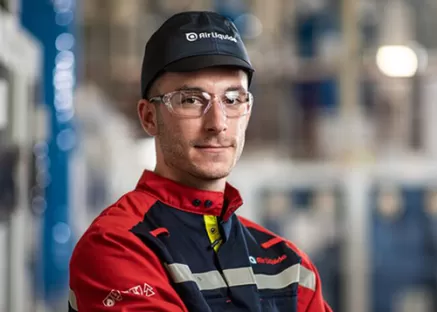
Our technical expertise at your service
Our experts support you in all stages of your project until the implementation and start-up of your solution, or even to advise you if your process were to evolve.
These specialists can:
- Intervene punctually or on a recurring basis to ensure optimal operation of your installations over time.
- Train your teams in gas safety (safety checks, use, and handling, etc.) as well as in the maintenance of your installation.
Air Liquide supplies the gases at the purity required for each different machine and application of the 3D printing process.
FAMILY | PROCESS | GAS | MATERIAL |
---|---|---|---|
Direct Energy Deposition |
LMD, DMD(1) |
Argon Nitrogen Helium |
Steels & all metallic materials |
Wire |
WAAM (2) | Range of industrial welding gases for MIG, MAG, TIG processes |
Steels & all metallic materials |
Selective powder bed fusion by aser or electron beam |
SLS (3) | Argon Nitrogen |
Plastics, other metal alloys |
SLM (4) ou DMLS |
Titanium, Aluminum, Steels, Chrome, Cobalt |
||
EBM (5) | Helium | All metallic materials |
|
Binder Metal Technologies |
BJT (6) | Sintering of powders under Argon (+ low % of hydrogen) Nitrogen |
All metallic materials |
Among the wide variety of processes used in industry sectors, the main ones are: (1) Laser Metal Deposition, Direct Metal Deposition (Cladding) (2) Wire Arc Additive Manufacturing (3) Selective Laser Sintering, or Direct Metal Laser Sintering (4) Selective Laser Melting (5) Electron Beam Melting 6) Binder Jetting Technology (Binder Metal or& Binder Metal Jetting) |