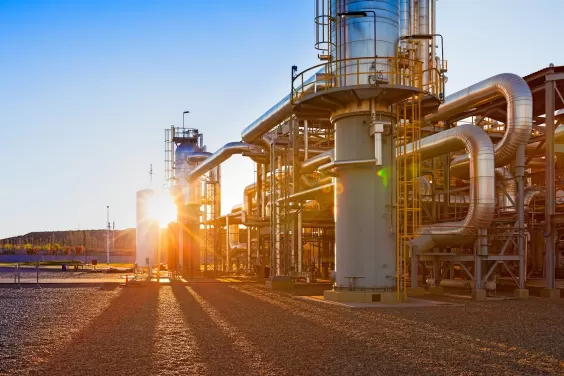
Guaranteeing shelf life for calibration gases used in emissions measurement equipment
11/09/2023
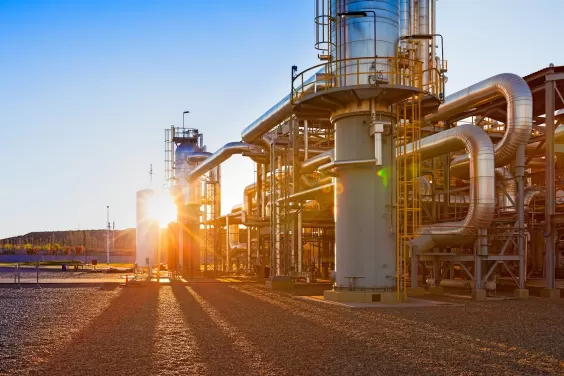
A stable solution for reactive and corrosive compounds
Compounds such as hydrogen chloride (HCI), hydrogen fluoride (HF), formaldehyde (CH2O), ammonia (NH3) and nitrogen dioxide (NO2) are highly reactive and corrosive. That’s why producing, storing, and using them properly is a challenge...
"Because they’re highly reactive, these compounds can react with the tiniest impurities, negatively affecting their stability," explains Simon James, Research & Analysis offer deployer at Air Liquide. "This leads to a shorter shelf life."
Assuring stability
"The point is that compound gases containing reactive components in low concentrations can react with moisture and oxygen, as well as with the internal cylinder surface. This causes degradation and eventually the compounds no longer meet their original specifications. But installations such as waste incinerators and cement plants rely on these compounds to calibrate their emissions measurement equipment to meet regulatory requirements."
The probability of a compound gas reaction depends on the cylinder material, how clean the cylinder is, how reactive its internal surface is, and how reactive the components of the compound are with each other. This means that a lot of different parameters have to be checked.
As a consequence, Air Liquide conducts extensive stability studies both internally and in cooperation with national metrology institutes. The company also has had years of investment in R&D studies to optimize cylinder and crane configurations. While these optimizations have significantly improved reliability, they have to be accompanied by special cylinder treatment techniques to achieve the best possible results.
Cylinder treatment
"There is no such thing as a universal approach to passivating a cylinder, and so a range of solutions has been developed to be applied depending on the various components and concentrations. So for a concentration of 100 ppb, we use a different approach than for a concentration of 100 ppm. The starting point is to remove all traces of moisture and oxygen, as well as other chemical substances that could react with the components. You could say that we want to make the cylinder "transparent" to the mixture. That way we stop the mixture becoming contaminated and thus extend shelf life."
Air Liquide's cylinder treatment programme includes various techniques based on the components and their concentration, such as: vacuuming, heat treatment, internal polishing, etching, or coating the cylinder to chemically modify the internal surface. These treatments are marketed under the Aculife and AlphaTech brand names.
"We also have a cylinder tracking and management system to ensure that we only use cylinders where we know exactly what compounds have been in them previously. We can then reuse the cylinders for the same application and avoid possible contamination. Last but not least, the cylinder valves are specially designed to stop unwanted substances getting in."
All these precautions and treatment options together ensure that the compound remains consistent and stable throughout its shelf life. Not surprisingly, Air Liquide is one of the leading treated cylinder suppliers for national metrology institutes. For example, NPL, the UK’s National Metrology Institute, uses Air Liquide's Aculife cylinder treatment (also AlphaTech and Megalife) to ensure the stability of many of the primary reference materials (PRMs) they produce.
Shelf life
"Shelf life claims for compounds — as much as ten years — are often exaggerated. The underlying idea is that these claims are proof of the manufacturer's level of know-how. But, in reality, extreme shelf life claims are inevitably accompanied by compromises in reliability."
"Air Liquide takes a different approach and in most cases offers a shelf life of three years, supported by scientific data. And it does this consistently around the world. A three-year shelf life offers the best trade-off in terms of price and duration of use, while ensuring the stability of the blend. This is also the opinion of most of our customers, including several national metrology institutes," Simon adds.
"Many of our customers regard our close cooperation with metrology institutes — such as NPL in the UK and VSL National Metrology Institute in the Netherlands — as a kind of seal of approval. We use reference materials from the metrology institutes, while they use our gases and our treated cylinders. So it really works both ways."